The real story behind the industrial dispute in Maruti factory that turned violent
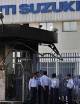
10-August-2012
Vol 3 | Issue 32
The Manesar (Haryana) plant of Maruti Suzuki India Ltd, a subsidiary of Suzuki Corporation of Japan and the largest car maker in the country, has been in the news for almost a year.
And for all the wrong reasons – the ongoing labour trouble which finally culminated in arson, rioting and the horrifying killing of a senior manager on July 18.
![]() |
40% of the Maruti Manesar workforce are contract or casual workers with a take-home of around Rs 6,000, and no paid leave (Infochange News & Features)
|
The mainstream media is packed with analysis on the causes of the unrest and advice for Maruti and other companies, but three important points have not received the attention they deserve.
1. The realities of Japanese management
The first is the fabled Japanese management. Not too long ago it was assumed that the Japanese have all the wisdom in manufacturing and management and if only we could learn from them we would find the answer to our woes.
Business schools worldwide teach special courses on ‘Japanese management’ and such offerings are highly subscribed; books on the subject are bestsellers.
But descriptions over the last one year of operations at Manesar demonstrate that essentially the Japanese trick to success is not so different from the rest: the principle followed is to get more work out of a worker, while at the same time paying less.
Accounts of Manesar tell of workers being forced to steal rest breaks, docking of pay for minor infringements, almost no paid holidays, an army of poorly-paid temps etc. Here is an account of a typical workday at Maruti Manesar (1):
You catch a bus at 5 am for the factory. Arriving a second late to punch in your card means a pay cut, but you can’t leave the premises once you’ve entered. At 6.30 am, you exercise and supervisors give you feedback on your previous output. Start work at 7 sharp. Everyone does his one task — assembling, welding, fixing — for a minimum of 8 continuous hours. A car rolls off the line every 38 seconds, which means you can’t budge from your position, ever. You get two breathless breaks during the day. At 9 am, a 7-minute break to drink tea or go to the loo, or both. After a while you might, like many of your friends here, end up taking your hot tea and kachori to the bathroom with you. Then a lunchbreak of 30 minutes, in which you walk about a half-kilometre to the canteen, wait in line with everyone, eat and walk back. Returning even a minute late from any break, or leaving the assembly line for any reason even for a minute, means half a day’s pay cut.
Overtime is a compulsion whenever the company needs it and the privilege of paid leave is a fantasy -- Rs 1,500 is deducted for one day’s leave (even when you intimate in advance) from a maximum possible monthly pay of Rs 16,000 and five days leave for any contingency reduces it to the base salary of Rs 8,000.
Out of a workforce of 2,500, 40% are on contracts, casual or apprentice (but do similar work as permanents) and their take-home is around Rs 6,000, with the threat of comparable deductions as regular workers looming all the time and no job security. Another worker states,
The problem is the immense pressure. They are extracting the work of 5,000 from half that number…(2)
And this is not unique to India. Such reports are corroborated by workers in Japan and Japanese plants in the US. For instance, a leading Japanese journalist worked for several months on the famed Toyota line in its prime during the 1970s and kept a diary which he later published as a book. This is how he concludes,
While management journalism may applaud Toyota’s high profit and the “kanban method”… the human costs of Toyota methods – suicides, injuries, job fatalities, and occupational disease – increase at a horrifying rate... Workers suffer every day in front of conveyer belts… this is the nightmare that I have lived…(3)
2. Union as intermediary between workers and management
The basic reason for the ongoing impasse of the last one year and its culmination in the grisly violence this July is the demand of the young Manesar workers to have their own representative union.
They did not want the union of the Gurgaon plant -- the parent plant where Maruti began its operations in the 1980s -- to represent them as they contended it was compromised and had failed to represent workers’ interests.
But the management insisted that the Gurgaon union was the true representative of the Manesar workers. Common sense tells us that each one of us should have the right to decide who can represent us, either individually or collectively.
The Constitution of India provides the ‘freedom to form association’ as a fundamental right and the Trade Union Act also gives a set of workers the right to form their own union.
But the Maruti management (and the Haryana government in collusion with them) systematically denied this basic right to the workers for the past year, rejecting them and frustrating them in every possible way – threats, coercion, force, enticements, etc.
Not only this: after a protracted process which continued for months, when the standoff was broken last year, the management in its wisdom decided to buy peace (literally) by dismissing the whole leadership of the agitation while simultaneously giving them hefty compensations.
According to media reports two top leaders were paid Rs 40 lakh each while 28 of them got Rs 16 lakh per person. Maruti Chairman Bhargava called this ‘voluntary retirement’ by young workers, most in their 20s, at the time!
What are the consequences of such a myopic outlook? When the crisis occurred on the morning of July 18 in the form of an altercation between a worker and a supervisor, there was no structure in place through which a management-worker dispute could be addressed – management had eliminated the whole set of leadership whom the workers trusted, there was no representative organisation which could have served as go-between and this kind of vacuum of leadership, organisation and trust set the stage for the unforgivable violence by the end of the day.
Though there was a new union registered and recognised in February this year, management had continued to undercut it in the same manner as before. I am not getting here into which side is more to be blamed for the events of that particular day – all I am saying is that once the mechanisms for a dialogue were systematically undermined, the preconditions for such an event were ever-present.
3. The elusive ‘spatial fix’
The third aspect is the persistent reports that Maruti is likely to move lock, stock and barrel to the investment haven of Narendra Modi’s Gujarat. Most revealing are the comments in the mainstream digital media: click on any news of the labour trouble this past one year and the comments section is full of unsolicited advice that Maruti should move from Haryana to Gujarat.
But the moot point is how come suddenly Manesar or Haryana have become unfriendly for Maruti? Wasn’t the ‘hardworking’, ‘docile’, and non-unionised labour of Haryana a big consideration when plants were established in Gurgaon in the 1980s and Manesar five years ago?
The geographer David Harvey calls this unceasing quest to relocate production to a favourable place an attempt at ‘spatial fix’.
But Beverly Silver (4) in a large study of the world auto industry from its inception to the 1990s demonstrates that along with the movement of the centre of auto production the location of labour unrest also shifts continuously.
The database reveals how the heart of labour unrest in the auto industry moved from North America in the 1930s and ’40s, to Western Europe in the 1960s and ’70s, and to developing countries in Latin America and East Asia in the 1990s.
Silver concludes, “where capital goes, conflict goes”. Perhaps the point can be more dramatically demonstrated through the opinion of Britain’s Blackburn mission of 1896 on Shanghai’s labour and the threat that it posed for British textiles (5):
Comparing this Oriental labour and our own, there is on the one hand, cheap, plentiful, submissive, capable labour (of Shanghai), plus the best machinery we can give it; on the other hand, dear, dictating and exacting labour (of GB), plus the same machinery. Can anyone call these equal conditions? Are they not in favour of Shanghai capitalist…?
However by the 1920s Shanghai was in the news for the ‘wrong’ reasons and workers in the industrial capital of China called a general strike in 1927 when several lakh workers and students fought together and finally the insurrection had to be quelled brutally by Chiang Kai-shek’s army.
There are no quick fixes for Maruti’s woes like moving to Gujarat or undermining the efforts of the workers to form their own unions.
Endnotes
(1) http://www.tehelka.com/story_main50.asp?filename=Ne240911Why.asp, all the accounts here of work and pay at Manesar are of last summers when the problems began gaining media attention.
(2) http://www.telegraphindia.com/1110612/jsp/frontpage/story_14103279.jsp
(3) Japan in the Passing Lane by Satoshi Kamata, Pantheon books, 1983.
(4) Beverly Silver, Forces of Labour, Cambridge Univ. Press, 2003. The study is based on a large data base created out of newspaper reports of labour unrest from 168 countries during 1870 to 1996.
(5) Quoted in Silver, p 88
(Rahul Varman is Professor, Department of Industrial and Management Engineering, IIT Kanpur) - Infochange News & Features